Изучение конструкции червячных редукторов. Описание устройства червячного редуктора
Введение
Качество продукции зависит от большого числа взаимосвязанных и не зависимых друг от друга факторов, имеющих как закономерный, так и случайный характер. Например, для машиностроительной продукции к числу таких факторов относят: точность оборудования; жесткость системы станок-приспособление инструмент-деталь; посторонние включения в материал заготовки; температурные колебания; квалификация обслуживающего персонала; погрешность режущего инструмента; режимы механической обработки; точность соблюдения параметров предварительной термической обработки и др.
В современном машиностроении существует большое разнообразие кинематических схем редукторов, их форм и конструкций.
Редукторы делятся на цилиндрические (оси ведущего и ведомого валов параллельны), конические (оси валов пересекаются), червячные (оси валов перекрещиваются в пространстве). Встречаются и комбинированные редукторы, представляющие сочетание зубчатых (цилиндрических и конических) и червячных передач.
По числу пар передач редукторы делятся на одноступенчатые и многоступенчатые.
Объектом данной курсовой работы является редуктор червячный одноступенчатый.
Целью курсовой работы является расширение, углубление и закрепление теоретических знаний, и применение этих знаний для проектирования технологических процессов сборки редуктора и технологических процессов изготовления детали – колесо червячное в сборе.
Характеристика и описание объекта разработки
Изделие – редуктор червячный, одноступенчатый. Редуктор состоит из чугунного литого корпуса, в котором на подшипниках качения вращаются валы с червяком и червячным колесом. Быстроходный вал выполнен заодно с червяком представляет собой вал-червяк. Червячное колесо посажено на валу на шпонку. Все валы вращаются на радиально-упорных роликовых подшипниках, поскольку осевая сила со стороны червячного зацепления довольно значительная. Подшипниковые узлы закрыты крышками с регулировочными прокладками, которые позволяют регулировать зацепление. Крышки подшипников на входном и выходном концах валов имеют резиновые уплотнения.
Корпус редуктора разъёмный и состоит из двух частей – верхней и нижней. Смачивание червячного зацепления осуществляется картерным непроточным способом – окунанием. Для этого в нижнюю часть корпуса заливается масло необходимой марки. Смазывание подшипников происходит в результате разбрызгивания масла. Уровень масла контролируется крановыми масло-указателями. На верхней крышке корпуса имеется крышка с пробкой-отдушиной, соединяющей внутреннею полость редуктора с атмосферой.
Редуктор предназначен для передачи и преобразования крутящего момента от электродвигателя через упругую втулочно-пальцевую муфту на приводной вал.
Для выполнения редуктором своего предназначения редуктор должен отвечать следующим требованиям:
1) детали должны быть точно изготовлены;
2) монтаж редуктора должен быть выполнен точно в соответствии с требованиями чертежа;
3) редуктор должен иметь высокий КПД и допускаемый уровень шума, что можно обеспечить точной сборкой зубчатых колёс.
Описание работы и служебное назначение объекта
Редуктор червячный одноступенчатый предназначен для передачи и преобразования крутящего момента от электродвигателя к валу рабочей машины.
Технические показатели редуктора:
1) Передаваемая мощность – 3,0 кВт;
2) Частота вращения входного вала – 1350 мин-1;
3) Передаточное число: редуктора – 15,5;
4) КПД редуктора – 74%;
5) Срок службы редуктора при двухсменной работе – 5 лет.
Редуктор получает вращение от электродвигателя через малоинерционную упругую муфту. При длительной работе без перерыва редуктора, температура трущихся деталей (колёс, валов и подшипников) не должна превышать 75°С, температура корпуса – 50°С. В связи с чем червяк редуктора погружается в масляную ванну. Смазывание подшипников происходит за счёт разбрызгивания.
Выбор и анализ НТД по качеству объекта разработки
Номенклатура показателей качества редукторов, обозначение и характеризуемые свойства приведены в ГОСТ 4.124-84 «Система показателей качества продукции. Редукторы, мотор - редукторы, вариаторы. Номенклатура показателей» Настоящий стандарт распространяется на редукторы, мотор - редукторы, вариаторы общемашиностроительного применения и устанавливает номенклатуру основных показателей качества, используемых при оценке уровня качества продукции.
Состоит из трех основных разделов:
1) Номенклатура показателей качества редукторов, мотор - редукторов, вариаторов.
2) Классификационные группировки редукторов, мотор - редукторов, вариаторов.
3) Применяемость показателей качества редукторов, мотор - редукторов, вариаторов.
Расчёт показателей качества
В соответствии с нормативно – технической документацией, указанной в предыдущем пункте данной курсовой работы, червячный редуктор имеет номенклатуру показателей, представленных в таблице 1.
Для достижения качественной работы передач редуктора необходимо:
1) Обеспечить кинематическую точность, т.е. согласованность углов поворота ведущего и ведомого колес передачи;
2) Обеспечить плавность работы, т.е. ограничение циклических погрешностей, многократно повторяющихся за один оборот колеса;
3) Обеспечить контакт зубьев, т.е. такое прилегание зубьев по длине и высоте, при котором, нагрузки от одного зуба к другому передаются по контактным линиям, максимально исполняющим всю активную поверхность зуба;
4) Обеспечить боковой зазор для устранения заклинивания зубьев при работе в передаче.
Таблица 1 – Показатели качества червячного редуктора
Наименование показателя | Обозначение показателя | Наименование характеризуемого свойства | |||
1. Показатели назначения | |||||
1.1. Классификационные показатели | |||||
1.1.1. Номинальная частота вращения входного вала, с - № | n вх. ном | - | |||
1.1.2. Номинальная частота вращения выходного вала, с - № | n вых. ном | - | |||
1.1.3. Передаточное число | U | - | |||
1.2. Функциональные показатели и показатели технической эффективности | |||||
1.2.1. Номинальный крутящий момент на выходном валу, Нм | М вых. ном | Нагрузочная способность | |||
1.2.2. Допускаемая радиальная консольная нагрузка, приложенная в середине посадочной части входного вала, Н | F вх. | Нагрузочная способность | |||
1.2.3. Допускаемая радиальная консольная нагрузка, приложенная в середине посадочной части выходного вала, Н | F вых. | Нагрузочная способность | |||
1.3. Конструктивные показатели | |||||
1.3.1. Удельная масса, кг/Н∙м | - | Эффективность использования материала в конструкции | |||
1.3.2. Габаритные размеры (длина, ширина, высота), мм | L∙B∙H | - | |||
1.3.3. Межосевое расстояние, мм | a w | - | |||
1.3.4. Климатическое исполнение и категория размещения | - | Стойкость к воздействию климатических | |||
2. Показатели надежности | |||||
2.1. Показатели безотказности | |||||
2.1.1. Установленная безотказная наработка, ч (ГОСТ 27.002-83) | Т у | Безотказность | |||
2.2. Показатели долговечности | |||||
2.2.1. Полный средний срок службы, год (ГОСТ 27.002-83) | Т сл | Долговечность | |||
2.2.2. Полный установленный срок службы, год (ГОСТ 27.002-83) | Т сл. у | Долговечность | |||
2.2.3. Полный девяностопроцентный ресурс передач, ч (ГОСТ 27.002-83) | Т р | - | |||
2.3. Показатель ремонтопригодности | |||||
2.3.1. Удельная суммарная трудоемкость технического обслуживания, чел. – ч/ч (ГОСТ 27.002-83) | S т.о | Ремонтопригодность | |||
3. Показатели унификации | |||||
3.1. Коэффициент применяемости, % | К пр | Степень заимствования | |||
3.2. Коэффициент повторяемости, % | К п | Степень повторяемости | |||
4. Эргономические показатели | |||||
4. Корректированный уровень | L ра | Звуковое давление | |||
звуковой мощности, дБА | |||||
5. Патентно – правововой показатель | |||||
5.1. Показатель патентной защиты | Р п.з. | Патентная защита | |||
5.2. Показатель патентной чистоты | Р п.ч. | Патентная чистота | |||
6. Показатель экономичного использования энергии | |||||
6.1. Коэффициент полезного действия, % | з | Эффективность использования энергии |
Для достижения поставленных целей редуктор должен иметь соответствующие единичные и комплексные показатели качества. Все показатели качества редуктора разрабатываются на такой стадии жизненного цикла изделия, как проектирование.
Обеспечение качества изделия при сборке. Выбор метода достижения качества
Обеспечение требуемого качества изделий, в том числе (и прежде всего) показателей назначения, технологичности и надежности, определяется достижением заданных параметров замыкающих звеньев размерной цепи.
Именно с этой целью выявлены размерные цепи и их уравнения, устанавливающие функциональные связи замыкающих и составляющих звеньев.
Размерные цепи отражают объективные размерные связи в конструкции машины, в технологических процессах изготовления её деталей и сборки, при измерении, возникающие в соответствии с условиями решаемых задач.
Свойства и закономерности размерных цепей отражаются системой понятий и аналитическими зависимостями, позволяющими рассчитывать номинальные размеры и обеспечивать наиболее экономичным путем точность изделий при конструировании, изготовлении, ремонте и во время эксплуатации.
Существует несколько методов достижения заданной точности исходного звена: метод полной взаимозаменяемости, вероятностный метод, метод регулирования.
Выявляем размерную цепь. Для нормальной работы в зацеплении должен оставаться зазор, который обеспечивается за точности изготовления и сборки редуктора.
Для обеспечения качества сборки необходимо соблюдать линейные размеры редуктора. Размерные цепи А, Б, В представлены на рисунке 1.
Размерная цепь Б: Б1 – соосность вала-червяка;Б2 – соосность подшипника; Б3– соосность колеса;Б4 – соосность подшипника; Б3 – межосевое расстояние.
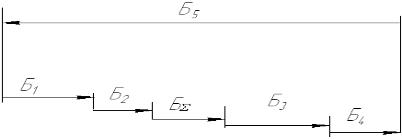
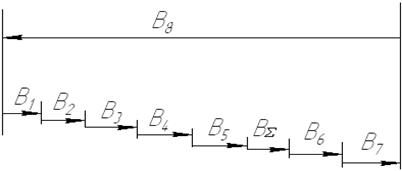
Рисунок 1 - Размерные цепи А, Б, В
Строим схему размерной цепи В, точность замыкающего звена которой была рассчитана ранее.
Звено В8 – увеличивающее.
В1, В2, В3, В4, В5, В6, В7 – уменьшающие
Номинальные значения звеньев
В1=9мм – фланец крышки; В2=5мм – втулка; В3=30мм – подшипник;
В4=10мм – бурт вала; В5=90мм – колесо; В6=30мм – подшипник;
В7= фланец крышки; В8=198 – расстояние между торцами корпуса.
Выполняем расчёт размерной цепи В различными методами точности.
Расчёт РЦ на максимум- минимум.
Постановка задачи. Имеется РЦ, состоящая из n составляющих звеньев, причём m из них увеличивающие. Назначить допуски одного или двух соседних квалитетов на составляющие размеры, причём размер замыкающего звена должен находиться в заданном интервале, равном ТБS.
Исходя, из условия замкнутости РЦ через замыкающее звено определим его номинальное значение по формуле
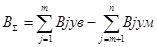
Где, j=1, 2, 3 n – номера составляющих звеньев.
Допуск на зазор равен
ТВS= ВSmax-ВSmin=888–0=0,888мм
Верхнее предельное отклонение замыкающего звена ES ВS равно
ВSmax-ВS=10,888–10=0,888мм
Нижнее предельное отклонение EI ВS равно
ВSmin-ВS=10,0–10,0=0,0мм
Таким образом, значение зазора можно записать как
ммКоордината середины поля допуска ЕсВS равна

Для того чтобы допуски на составляющие размеры назначить из одного квалитета, необходимо рассчитать коэффициент точности РЦ
(2)Где, ij единица допуска интервала, в который входит j-ый размер.
Если в РЦ имеются звенья с известными допусками (например, кольца подшипников 0,120мм, формула для арасч (2) должна быть скорректирована:
В числителе допуск замыкающего звена, зависящий только от размеров, допуски на которые не известны, а в знаменателе сумма единиц допуска для этих размеров.
Сравнивая значения арасч с атаб, определяем требуемый квалитет, из которого назначаем допуски на составляющие звенья. При этом учитываем координаты полей допусков.
Назначаем допуски на составляющие размеры из 10 квалитетов, кроме размера В2.
В1=9-0,058мм; В4=10-0,058мм; В5=90-0,140мм; В7=14-0,07мм; В8=198+0,185мм
Допуски равны
ТВ1=58мкм; ТВ4=58мкм; ТВ5=140мкм; ТВ7=70мкм; ТВ8=185мкм
esВ1=-29; esВ4=-29; esВ5=-70 ecВ7=-35 ESB8=92,5
Определим допуск ТВ2 по (1).
ТBS =ТB1+ТB2+ТB3+ТB4+ТB5+ТB6+ТB7+ТB8
ТB2=ТBS-(ТB1+ТB2+ТB3+ТB4+ТB5+ТB6+ТB7+ТB8)=888–(58+58+120+120+140+70+185)=137 мкм
Из формулы
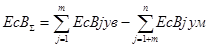
ЕсBS=ЕсB8–есB1-есB3-есB4–есB5–есB6–есB7–есB2
eсB2=-ЕсBS+ЕсB8–(есB1+есB3+есB4+есB5+есB6+есB7)=-444 +92,5-(-29-29-70-35-60-60)=0+0+0+0 =-68,5мкм

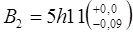
Проверочный расчёт РЦ на максимум-минимум:
Номинальное значение замыкающего звена равно:
BS=B8–B1–B2–B3–B4–B5–B6–B7=198-9-30-10-90-10-30-14=5мм
ТBS=ТB1+ТB2+ТB3+ТB4+ТB5+ТB6+ТB7+ТB8=58+90+120+58+140+120+70+185=841мкм
мкм(7)
ВSmax=ВS+ESВS=5+0,881=5,881мм
ВSmin=ВS+EI ВS=0–0,0=0,0мм
Результаты сводим в таблицу 2
Таблица 2 - Данные для расчета размерной цепи
Размер | В1 | В2 | В3 | В4 | В5 | В6 | В7 | В8 | ВS |
Номинальное значение, мм | 9 | 5 | 30 | 10 | 90 | 30 | 14 | 198 | 10 |
Ec (ec) | -29 | -45 | -60 | -29 | -70 | -60 | -35 | 92,5 | 420,5 |
ES (es) | 0 | 0 | 0 | 0 | 0 | 0 | 0 | 185 | 841 |
EI (ei) | -58 | -90 | -120 | -58 | -140 | -120 | -70 | 0 | 0 |
Проверка показала, что назначенные предельные отклонения составляющих звеньев обеспечивают требуемую точность замыкающего звена, однако принадлежность их квалитету IT10 делает изготовление деталей экономически не выгодным.
Расчёт размерных цепей вероятностным методом
Имеем ту же размерную цепь, состоящую из n составляющих звеньев, причём m из них увеличивающие. Необходимо назначить более экономичные, чем в первом случае расширенные допуски одного или двух соседних квалитетов на составляющие размеры. Размер замыкающего звена должен находиться в заданном интервале, равном ТБS, причём имеется заранее известный процент риска выхода размера замыкающего звена за границы этого интервала.
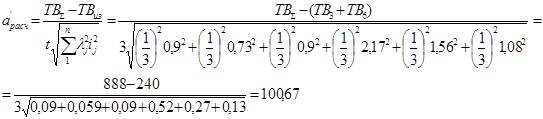
Где,t коэффициент риска, определяемый по принятому проценту риска. При нормальном распределении размеров замыкающего звена
lj – коэффициент относительного рассеяния. При нормальном законе распределения
Назначаем допуски на составляющие размеры из 11 квалитета, кроме размера В2.
В1=9-0,09мм; В4=10-0,09мм; В5=90-0,22мм; В7=14-0,11мм; В8=198+0,290мм
Допуски равны
ТВ1=90мкм; ТВ4=90мкм; ТВ5=220мкм; ТВ7=110 мкм; ТВ8=290мкм
Координаты середин полей допусков равны, (мкм)
esВ1=-45мкм; esВ4=-45мкм; esВ5=-110мкм ecВ7=-55мкм
Определим допуск ТБ5 из уравнения
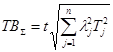
После преобразования и подстановки
Откуда имеем
Определим координату середины поля допуска размера
eсB2=-ЕсBS+ЕсB8–(есB1+есB3+есB4+есB5+есB6+есB7)=-444+145-(-45-45-110-55-60-60)=0+0+0+0=76мкм
Определим предельные отклонения размера B2 по формулам


Допуск на межосевое расстояние будет иметь вид.
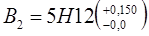
Проверочный расчёт РЦ вероятностным методом
Допуск замыкающего звена
мкмЗначения нижнего и верхнего предельных отклонений замыкающего звена равны:
мкм(6) мкмНаибольший и наименьший зазоры равны:
ВSmax=ВS+ESВS=10+0,817=10,817мкм
ВSmin=ВS+EIВS=100,373=10,373мкм
Результаты сводим в таблицу 3
Таблица 3 - Данные для расчета размерной цепи
Размер | В1 | В2 | В3 | В4 | В5 | В6 | В7 | В8 | ВS |
Номинальное значение, мм | 9 | 5 | 30 | 10 | 90 | 30 | 14 | 198 | 10 |
Ec (ec) | -45 | 75 | -60 | -45 | -110 | -60 | -55 | 145 | 420,5 |
ES (es) | 0 | 150 | 0 | 0 | 0 | 0 | 0 | 290 | 595 |
EI (ei) | -90 | 0 | -120 | -90 | -22 | -120 | -110 | 0 | 373 |
Проверка показала, что назначенные предельные отклонения составляющих звеньев обеспечивают требуемую точность замыкающего звена, и принадлежность их квалитету IT11 экономически более целесообразно, чем IT10.
Расчёт размерных цепей методом компенсаторов.
Под методом регулирования понимают такой расчёт размерных цепей, при котором предписанная точность исходного (замыкающего) звена достигается преднамеренным изменением (регулированием) величины одного из заранее выбранных составляющих размеров, называемого компенсирующим. Роль компенсатора обычно выполняет специальное звено в виде прокладки, регулируемого упора, клина или втулки. При этом по всем остальным размерам цепи детали обрабатывают по расширенным допускам, экономически приемлемых для данных производственных условий. Недостатком такого расчёта является усложнение конструкции. Примером компенсатора может являться набор сменных прокладок, вводимых в сборочную размерную цепь.
Назначаем расширенные допуски на составляющие звенья по IT12
В1=9-0,15мм; В4=10-0,15мм; В5=90-0,35мм; В7=14-0,18мм; В8=198+0,460мм
Допуски равны
ТВ1=150мкм; ТВ4=150мкм; ТВ5=350мкм; ТВ7=180мкм; ТВ8=460мкм
Координаты середин полей допусков равны, (мкм)
esВ1=-75мкм; esВ4=-75мкм; esВ5=-175мкмecВ7=-90мкм
ESB8 = 230 мкм
Звено В2 (втулка) – компенсатор.
Диапазон компенсации
мкм(9)Для Бk уменьшающего координата середины поля допуска

Предельные отклонения Бk


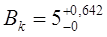
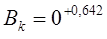
Предельные отклонения
мкмОтклонения найдены, верно.
Рассчитаем число и толщину прокладок. Размер Вkmin можно принять за толщину постоянной прокладки Sпост = 5,0 мм. Число сменных прокладок
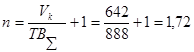
Принимаем n=2, тогда толщина сменных втулок
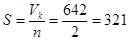
Расчёт проверяем по формулам
Sпост£Вkmin
Sпост+nS³Вkmax
0+2×0,35 =0,7³0,642
Вк1=5,35+0,05мм
Вк2=5,7+0,05мм
Выбор вида и формы организации процесса сборки
Сборка является одним из заключительных этапов изготовления изделия, в котором сходятся результаты всей предшествующей работы, проделанной конструкторами и технологами по созданию изделия. Качество изделия и трудоемкость сборки во многом зависят от того, как понято конструктором и воплощено в конструкции служебное назначение изделия, как установлены нормы точности, насколько эффективны выбранные методы достижения требуемой точности изделия и как отражены эти методы в технологии изготовления изделия. Технолог, разрабатывающий технологический процесс сборки изделия, должен: отчетливо представлять задачи, для решения которых создается изделие; понимать связи, посредством которых изделие должно выполнять предписанный ему процесс; обеспечить с требуемой точностью все необходимые связи в изделии соответствующим построением технологического процесса его изготовления, предъявив требования сборки к технологии изготовления деталей и контролю их точности.
Решающим фактором выбора вида сборки является количество машин подлежащих изготовлению в единицу времени. По своему объему сборка подразделяется на общую и узловую.
Поточная сборка более производительна, сокращает цикл производства и межоперационные заделы, повышает специализацию сборщиков. А также возможность механизации и автоматизации сборочных работ. При поточной сборке перемещении от собираемого объекта от одного рабочего места к другому осуществляют:
1) Вручную
2) При помощи механических транспортирующих устройств, используемых в основном для многооперационного перемещения собираемых объектов.
3) На конвейере периодическим перемещением (пластинчатый конвейер), тележки, ведомые по рельсовому пути замкнутой цепи, в этом случае сборку проводят на конвейере в периоды его остановки.
4) На непрерывно движущемся конвейер, который перемещает изделия с такой скорости, чтобы можно было на определенных участках совершать различные сборочные операции.
Поточную сборку машин больших габаритных размеров и массы экономичнее собирать, оставляя их неподвижными и периодически перемещая бригадой рабочих от одной машины к другой. Сборка обычно проводится на неподвижных стендах. Такая форма сборки широко используется в серийном производстве.
С уменьшением количества машин подлежащих изготовлению, когда поточная сборка становится не экономичной, применяют не поточную сборку, в мелкосерийном производстве широко применяется групповая сборка, которая позволяет использовать технологические и организационные достоинства крупносерийного производства в части применения поточных методов работы сокращения трудоемкости и себестоимости сборки, использования высокопроизводительного оборудования, средств механизации и автоматизации. В групповой поточной линии оборудование располагают по технологическому маршруту сборки узлов. Группы подбираются по признакам технологической общности и серийности выпуска.
Для группы разрабатывают технологический процесс и проектируют наладки оборудования. Может производиться одновременная групповая сборка всех прикрепленных к данной сборочной позиции узлов, при ее временной наладке. При этом применяют специальные приспособления, в которые устанавливают все узлы, собираемые на данной операции.
Разработка технологической схемы сборки
Схема сборки рассматриваемого одноступенчатого цилиндрического редуктора представлена в графической части.
Перед сборкой внутреннюю полость корпуса редуктора очищают и покрывают краской. Сборку производят в соответствии со сборочным чертежом редуктора.
Сначала запрессовывают шпонки, затем надевают колесо и запрессовывают подшипники. В крышки закладывают масло удерживающие кольца.
Собранные валы укладывают в основание корпуса редуктора и надевают крышку корпуса, покрывая предварительно поверхности стыка крышки и корпуса спиртовым лаком. Устанавливают закладные крышки. Для центровки устанавливают крышку на корпус с помощью двух диагонально расположенных штифтов и затягивают болты.
Заливают в корпус масло и закрывают крышку.
Собранный редуктор обкатывают и подвергают испытаниям на стенде.
Для нормальной работы шариковых и роликовых подшипников следует следить, чтобы вращение подвижных элементов (внутренних колец) происходило легко и свободно, с другой стороны, чтобы в подшипниках не было излишне больших зазоров. Это достигается с помощью регулировки, для чего применяют наборы тонких металлических прокладок, устанавливаемые под фланцы крышек подшипников или втулок. Необходимая толщина набора прокладок может быть составлена из тонких металлических колец.
редуктор показатель технологический схема
Разработка операционного технологического процесса сборки
Заключительным этапом технологического процесса сборки машины является нормирование сборочных работ, определение трудоемкости сборки и компоновка операций из переходов.
Установленные нормы времени на сборку отдельных сборочных единиц и машины в целом дают возможность определить трудоемкость их сборки как сумму затрат времени на выполнение отдельных переходов.
Значение трудоемкости переходов и необходимого числа рабочих дает возможность объединить переходы и тем самым сформировать операции. Каждая операция должна представлять собой законченную часть технологического процесса, выполняемую рабочим или бригадой рабочих на отдельном рабочем месте. Для определения длительности сборки машин строят циклограмму. Циклограмма позволяет вскрыть пути сокращения цикла сборки, что важно для уменьшения объема незавершенного производства.
Циклограмма сборки. Планировка участка
Циклограмма – это графическое определение последовательности выполнения операций, переходов или приёмов сборочного процесса и затрат времени на их выполнение. При построении циклограммы в вертикальной колонке построчно записывают все операции, переходы и приёмы. Степень их дифференциации зависит от уровня циклограммы.
Циклограмма сборки в соответствие со схемой сборки представлена на рис. 2
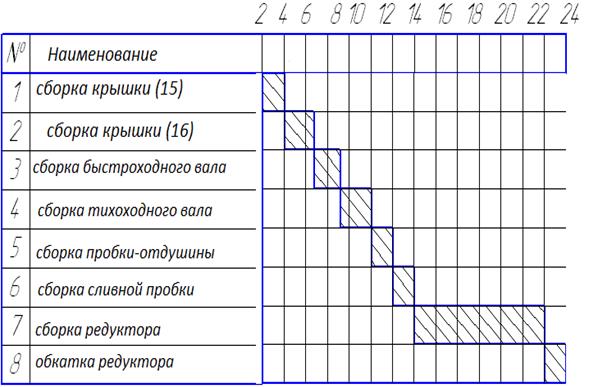
Рисунок 2 - Циклограмма сборки.
Технологический процесс изготовления детали. Характеристика и служебное назначение детали
Деталь «колесо червячное» (рисунок 3) представляет собой тело вращения и имеет габаритные размеры Ш 229 Ч 90. Деталь предназначена для приёма вращения от червяка.
Наиболее точными поверхностями детали являются:
Отверстие Ш60 Н7 с шероховатостью Ra = 1,6 мкм.
Паз b = 18 Js9 с шероховатостью Ra = 3,2 мкм.
Зубчатый венец Ш229h12 с шероховатостью зубьев Ra = 1,6 мкм.
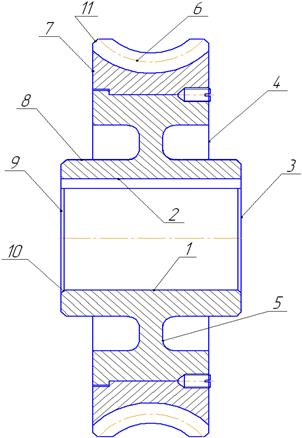
Рисунок 3 – Колесо червячное в сборе
Каждому элементу детали назначаем порядковый номер и технические требования согласно рабочему чертежу и заносим в таблицу 4.
Конструкция детали «колесо червячное» - сборное, поэтому на предварительном этапе заготовку ступицы для детали можно предложить полученную штамповкой на горизонтально-ковочных машинах. Бронзовый венец получают отливкой. После запрессовки венца на ступицу деталь обрабатывается.
Таблица 4 - Анализ конструкции зубчатого колеса
Наименование поверхности, размер | Точность |
Шероховатость поверх., Ra, |
Назначение поверх | |
1 | 2 | 3 | 4 | 5 |
1 | Отверстие |
H7 | 1,6 | Конструкторская |
2 | Паз b = 18 мм | Js9 | 3,2 | конструкторская |
3 | Торец | h 12 | 2,5 | конструкторская |
4 | торец | h 14 | 6,3 | свободная |
5 | выемка | Н14 | 6,3 | свободная |
6 | Венец зубчатый |
h 8 | 1,6 | конструкторская |
7 | торец | h 14 | 6,3 | свободная |
8 | Наружный диаметр | Н14 | 6,3 | свободная |
9 | Торец | h 12 | 2,5 | конструкторская |
10 | Фаска, 1,6Ч45є | h 14 | 6,3 | свободная |
11 | Фаска, 3,0Ч45є | h 14 | 6,3 | свободная |
Деталь обладает достаточной жёсткостью, так как отношение её длины к диаметру менее 10,
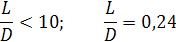
Конструкторская жёсткость детали позволяет обрабатывать ее, используя обычные режимы резания, а также нет необходимости для применения устройств (люнетов), служащих для увеличения жёсткости системы обработки.
Все поверхности детали открыты для её обработки резанием и позволяют применять стандартные режущие инструменты. В целом конструкция детали технологична и при создании необходимых условий обработки, трудностей при её изготовлении не возникнет.
Показатели качества детали
Колесо червячное предназначено для передачи и преображения крутящего момента, для этого на его внешнем диаметре нарезаны зубья. Для передачи крутящего момента предназначен шпоночный паз. Для нормальной работы червячное колесо должно плотно сидеть на валу, поэтому его внутренний диаметр выполнен по посадке Æ60Н7, что достигается шлифовкой. Чтобы колесо легко собиралось, необходимо обеспечить следующие требования, предъявляемые к шпоночному пазу: допуск симметричности 0,016 мкм, допуск параллельности 0,028мкм относительно оси отверстия.
Точность остальных размеров находится в пределах 14 квалитета точности. Шероховатость шпоночного паза составляет Ra=3,2мкм и может быть обеспечена во время протягивания. Шероховатость оставшихся поверхностей Ra=6,3мкм и не требует чистовых и доводочных операций.
Выбор заготовки и способа её изготовления
Определяем коды материала, серийности производства, конструктивной формы и массы заготовки.
1) Материал. По табл. 3.1 для Стали 45 определяем код – 6 (легированные стали).
2) По табл. 3.3 – серийность
Вид заготовки – штамповка, поковка
Масса – 6,1 кг
Годовая программа выпуска – 2500 шт.
3) Определяем конструктивную форму по чертежу по табл. 3.2 – код 3: детали типа дисков.
4) По табл. 3.4 определяем код массы – 4.
Имеем следующие обозначение заготовки 6-3-3-4
7 – штамповка на молотах и прессах;
8 – штамповка на горизонтально-ковочных машинах;
9 – Свободная ковка.
Методы получения заготовок:
1) Штамповка на молотах или штамповка на прессах;
2) Штамповка на горизонтально-ковочных машинах;
3) Свободная ковка.
Штамповка на молотах и прессах
Масса заготовки
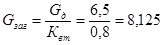
где Квт =0,8 (табл. 3.5 ), Gд = 6,5 кг
рубЦ1 = 463 руб, Ц2 = 446 руб, М1= 5,65 кг, М2 = 8,5 кг (табл. 3.4 )
Стоимость заготовки
руб.Кто=25 для нормализации, Кт=1,0; Кс= 1,3 (табл. 3.9 )
Штамповка на горизонтально-ковочных машинах
Масса заготовки
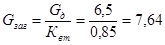
где Квт =0,85 (табл. 3.1 ), Gд = 6,5 кг
Базовая стоимость 1 т заготовок
рубЦ1 = 463 руб, Ц2 = 446 руб, М1= 5,65 кг, М2 = 8,5 кг (табл. 3.4)
Стоимость заготовки
руб.Кто=25 для нормализации, Кт = 1,0; Кс = 1,0 (табл. 3.9 )
Свободная ковка
Масса заготовки

где Квт =0,6 (табл. 1), Gд = 6,5 кг
Базовая стоимость 1 т заготовок
Ц1 = 424 руб, Ц2 = 387 руб, М1= 5,65 кг, М2 = 10 кг (табл. 3.4 )
Стоимость заготовки
руб.Кто = 25 для нормализации, Кт = 1,0; Кс = 1,0 (табл. 3.9 )
Выбираем получение заготовок на горизонтально-ковочных машинах, Сзаг = 13,46 руб
Определение типа производства
Согласно ГОСТ 3.1108-74 ЕСТД и ГОСТ 14.004-74 ЕСТД одной из основных характеристик типа производства является коэффициент закрепления операций Кз.о.
Коэффициент Кз.о показывает отношение числа всех операций, выполняемых в цехе в течение месяца, к числу рабочих мест, т.е. характеризует число операций, приходящихся в среднем на одно рабочее место в месяц, или степень специализации рабочих мест.
При Кз.о £ 1 производство является массовым
1£Кз.о £ 10 – крупносерийным;
10£Кз.о £ 20 - среднесерийным;
20£Кз.о £ 40 – мелкосерийным.
В единичном производстве Кз.о не регламентируется.
Упрощёно, тип производства можно определить по массе детали и годовой программе выпуска. При массе 6,5 кг и годовой программе выпуска 2500 штук в год тип производства – средне-серийное.
Разработка маршрутного технологического процесса. Выбор общих технологических баз
Для детали колесо червячное в собре выбираем следующие технологические базы: установочная (1, 2, 3), двойная опорная (4, 5), опорная (6) (рисунок 4). Такое базирование обеспечит заданную точность в процессе изготовления детали и будет обеспечена при базировании на оправке и в мембранном патроне при шлифовании внутреннего диаметра колеса. Для первой операции выбираем базирование в центровой оправке.
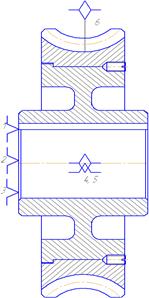
Рисунок 4 – Схема базирования колеса червячного в сборе
Разработка последовательности выполнения операций
Разработка последовательности выполнения операций – это, так называемый, маршрут обработки заготовки, который представлен в таблице 5.
Таблица 5 - Технологические схемы обработки
Наименование поверхности |
Технологические переходы |
Требуемые параметры |
||
IT | Ra | |||
1 | Зубчатая поверхность, D = 229 |
Точение черновое Точение чистовое Фрезерование зубьев Обкатывание зубьев |
||
2 | Торец | Без обработки | Н14 | 6,3 |
3 | Выемки | Без обработки | Н14 | 6,3 |
4 | Внешний диаметр Æ 90 | Без обработки | Н14 | 6,3 |
5 | Торец L= 90 | Точение однократное | h12 | 2,5 |
6 | Фаска 1,6 ´ 45° | Точение однократное | h14 | 6,3 |
7 | Шпоночный паз |
протягивание | Js9 | 3,2 |
8 | Внутренняя цилиндрическая поверхность, D = 60 |
Зенкерование черновое Зенкерование чистовое Протягивание Шлифование черновое Шлифование чистовое |
||
9 | Торец | Без обработки | ||
10 | Торец L= 90 | Точение однократное | h14 | 6,3 |
11 | Торец L= 70 | Точение однократное | h12 | 2,5 |
Проектирование операционного технологического процесса. Выбор оборудования и СТО
Оборудование и их технические характеристики представлены в таблице 6.
Таблица 6 – Технологическое оборудование
Наименование операции | Модель станка |
Токарная | Токарно-винторезный станок модели 16К20 Параметры: Наибольший диаметр обрабатываемого прутка 400 мм Наибольшая длина подачи прутка 1000 мм Частота вращения шпинделя 12.5 – 1600 об/мин Продольная подача револьверного суппорта 0.05 – 2.8 мм/об Мощность эл. двигателя привода главного движения 11 КВт |
Протяжная | Горизонтально - протяжной станок модели 7Б510 Параметры: Номинальное тяговое усилие 10000 кг-с Длинна рабочего хода ползуна 1250 мм Диаметр отверстия под планшайбу в опорной плите 150 мм Размер передней опорной плиты 420 мм Пределы рабочей скорости протягивания 1¸9 м/мин Мощность главного электродвигателя 17 кВт КПД станка 0,9 |
Внутришлифо- |
Внутришлифовальный станок модели 3К225В Параметры: Наибольшие размеры устанавливаемой заготовки диаметр 200 мм длина 50 мм Диаметр шлифуемых отверстий 3-25 мм Наибольший ход стола 320 мм Частота вращения шпинделя заготовки 280 – 2000 об/мин Частота вращения шпинделя шлиф. круга 20000 об/мин Мощность электродвигателя привода главного движения |
Зубофрезерная | Зубофрезерный полуавтомат модели 5304В Параметры: Наибольший диаметр обрабатываемой заготовки 80 мм Наибольшие размеры нарезаемых колес: модуль 1,5 длина зуба прямозубых колес 100 мм Частота вращения шпинделя инструмента 1600 об/мин Мощность электродвигателя привода главного движения 1,5 кВт |
Зубообкотная | Зубообкатной станок модели 5П722 Параметры: Наибольший диаметр обрабатываемой заготовки 320 мм Модуль обрабатываемых зубчатых колес 0,3-6 Частота вращения ведущего шпинделя 1450 об/мин Мощность электродвигателя привода главного движения 5,5 кВт |
Для обработки шестерни на различном оборудовании выбираем стандартный металлорежущий инструмент и заносим его в таблицу 7.
Таблица 7 – Металлорежущий инструмент
Формирование структуры операций и построение размерных схем
При современном уровне требований к изделиям машиностроения высокие показатели качества деталей машин, как правило, могут быть достигнуты лишь путем ряда последовательно выполняемых технологических операций. Свойства деталей формируются поэтапно – от операции к операции, поскольку для каждого способа обработки существуют возможности исправления исходных погрешностей заготовки и получения требуемых точности и качества обработанных поверхностей. Поэтому, как отмечалось ранее, при изготовлении заготовки необходимо стремиться, чтобы она по форме и размерам максимально приближалась к готовой детали. Это приводит к повышению точности и качества поверхностей готовой детали, способствует экономии материала и сокращению трудоемкости механической обработки. Для достижения поставленной задачи – обеспечения заданных показателей редуктора – следует правильно назначить припуски и допуски на заготовку рассматриваемого червячного колеса.
0,2Технологическое установочно-зажимное приспособление. Служебное назначение приспособления
Для чистовой обработки наружной поверхности и шлифования колесо надеваем на центрирующую оправку, которая обеспечит заданную точность установки.
Центровые оправки применяют для установки с центральным базовым отверстием втулок, колец, шестерён, обрабатываемых на многорезцовых шлифовальных и других станках. При обработке партии таких деталей требуется получить высокую концентричность наружных и внутренних поверхностей и заданную перпендикулярность торцов к оси детали.
Показатели качества приспособления
При базировании на центрирующей оправке на чистовых операциях и при обработке зубьев заготовка устанавливается по обработанному внутреннему диаметру, что позволяет избежать погрешностей базирования, поскольку обеспечивает взаимосвязь между зубчатой поверхностью и осью посадочного отверстия. При выбранной схеме базирования заготовки на центрирующей оправке технологическая, конструкторская база и измерительная совпадают, что приведет к отсутствию погрешности базирования.
Для оправки с тарельчатыми пружинами погрешность установки
мкм при базе в 150 ммИзнос при обработке колеса при базировании на тарельчатые пружины
Погрешность фиксации
Принципиальная схема и описание работы приспособления. Оправки и патроны с тарельчатыми пружинами применяются для центрирования и зажима по внутренней или наружной цилиндрической поверхности обрабатываемых деталей. В графической части показана центровая оправка с тарельчатыми пружинами. Оправка состоит из корпуса 7, упорного кольца 2, пакета тарельчатых пружин 6, нажимной втулки 3 и тяги 1, и гайкой 4. Оправку применяют для установки и закрепления детали 5 по внутренней цилиндрической поверхности. При закручивании гайки 4, последняя, через втулку 3, нажимает на тарельчатые пружины 6. Пружины выпрямляются, их наружный диаметр увеличивается, а внутренний уменьшается, и обрабатываемая деталь 5 центрируется и зажимается.
Заключение
В результате проделанной работы были реализованы навыки ведения самостоятельной инженерной работы, изучена методика теоретико-эксперементальных исследований технологических процессов механо-сборочного производства.
Осуществлено проектирования технологических процессов сборки редуктора червячного одноступенчатого и технологических процессов изготовления детали – колесо червячное в сборе.
Список использованных источников
1. Маталин А.А. Технология машиностроения. Л.: Машиностроение, Ленингр. Отд-ние, 1985г. 496с.
2. Аверченков В.И., Гордиленко О.А. и др. Сборник задач и упражнений по технологии машиностроения. М: Машиностроение, 1988г. 192с.
3. Руцкой A.M., Шишков С.Е. и др. Сборник задач и упражнений по технологии машиностроения. Курск ГТУ. Курск, 2000г. 240с.
4. Справочник контролёра машиностроительного завода. Допуски, посадки, линейные измерения/ А.Н. Виноградов, Ю.А. Воробьёв, Л.Н. Воронцов. М.: Машиностроение. 1980г. 527с.
5. Справочник технолога-машиностроителя. Т. 1. /А.Г. Косилова, Р.К. Мещеряков. М.: Машиностроение. 1986г. 656с.
6. Справочник технолога-машиностроителя. Т. 2. /А.Г. Косилова, Р.К. Мещеряков. М.: Машиностроение. 1986г. 496с.
7. Якушев А.И. и др. Взаимозаменяемость, стандартизация и технические измерения. М.: Машиностроение, 1986г.
8. Допуски и посадки: Справочник под ред. Мягкова. Л.: Машиностроение, 1979г.
9. Белоусов А.П. Проектирование станочных приспособлений. М., «Высшая школа», 1974г. 264с.
10. Колесов И.М. Основы технологии машиностроения: Учеб. для машиностроит. спец. вузов. – 3-е изд., стер. – М.: Высш. шк., 2001г. 591с.: ил.
11. ГОСТ 29285 – 92 «Редукторы и мотор – редукторы. Общие требования к методам испытаний
Цель работы : изучить назначение и конструкцию червячных редукторов, определить геометрические, кинематические и энергетические параметры зацепления и редуктора, ознакомиться с конструкцией, особенностями регулировки зацепления, подшипников и их смазкой.
1. Общие сведения о конструкциях червячных редукторов
1.1. Характеристика червячных редукторов
Червячные редукторы предназначены для передачи вращения между перекрещивающимися валами с уменьшением угловых скоростей и увеличением вращающих моментов, когда ведущим является червяк. Реже вращающим может быть колесо, тогда угловая скорость увеличивается, а вращающий момент уменьшается. Червячная передача состоит из червяка и червячного колеса. Червяк является винтом, червячное колесо представляет собой разновидность косозубого колеса. Червячные передачи относят к категории зубчато-винтовых.
Рис. 1. Червячная передача.
Основными характеристиками редуктора являются передаточное число и вращающий момент на тихоходном валу.
Редукторы червячные одноступенчатые универсальные обдуваемые типа Ч обеспечивают передачу вращающих моментов =85…2000Н∙м в диапазоне передаточных чисел =8…80.
Промышленностью серийно выпускаются редукторы Ч-63, Ч-80, Ч-100, Ч-125, Ч-160. Буква Ч обозначает – редуктор червячный одноступенчатый, число – межосевое расстояние в мм.
Серийно выпускаются также и червячные универсальные двухступенчатые редукторы типа Ч2: Ч2-125; Ч2-160; числа – межосевые расстояния тихоходной ступени, которые обеспечивают передачу вращающих моментов на тихоходном валу =1300…2800Н∙м в диапазоне передаточных чисел =100…6300.
Достоинства червячных передач:
1) большие передаточные числа в одной ступени =8…80 в силовых передачах, до 1000 в приборах;
2) плавность и бесшумность работы;
3) высокая кинематическая точность в сравнении с зубчатыми передачами;
4) возможность передачи вращения между скрещивающимися валами;
5) возможность самоторможения.
Недостатки червячных передач:
1) низкий коэффициент полезного действия ( =0,4…0,9 для одноступенчатого редуктора) из-за значительного скольжения между поверхностями витков червяка и зубьев колеса;
2) сравнительно большие габариты передач, особенно при больших вращающих моментах вследствие значительно меньших величин допускаемых контактных напряжений;
3) необходимость применения дефицитных дорогостоящих сплавов цветных металлов для изготовления червячных колес.
1.2. Основные кинематические схемы червячных редукторов
1.2.1. Кинематический расчет
Передаточное отношение червячной передачи
Иными словами, передаточное отношение в червячной передаче, как и в зубчатой, численно равно передаточному числу . Так как число заходов червяка (число зубьев) , чего не может быть в зубчатой передаче, где =17, то в одной червячной паре можно получить передаточное число, значительно большее, чем в зубчатой, что является основным достоинством червячной передачи. При 2 минимальное число зубьев колеса по условию неподрезания = 2. В силовых передачах =8…80.
1.3. Конструкция одноступенчатого червячного редуктора
Рис. 2. Редуктор червячный одноступенчатый с вентилятором.
На рисунке 2 представлена конструкция одноступенчатого червячного редуктора с нижним расположением червяка с горизонтальной плоскостью разъема.
Оребренный корпус редуктора 1 болтами соединяется с крышкой 2, также имеющей ребра.
Вращающий момент от вала червяка 9 передается червячному колесу 12, а затем через шпоночное соединение тихоходному валу 13. Червячное колесо фиксируется от осевого перемещения по валу справа упорным буртиком вала, а слева – мазеудерживающим кольцом-втулкой 11.
Вал червяка фиксируется от осевого перемещения правой опорой с двумя радиально-упорными шарикоподшипниками, размещенными в стакане 5 – фиксирующая опора.
Левая опора вала-червяка с одним радиальным шарикоподшипником – плавающая.
Для смазывания червячного зацепления и одновременной защиты подшипников вала-червяка от попадания в них продуктов разрушения установлены брызговики-крыльчатки 8. На крышке редуктора для его транспортировки имеются проушины.
Лючок для заливки масла и осмотра зацепления закрыт крышкой-отдушиной 4.
Масло при его замене выливают через отверстие, закрытое пробкой 10 с резьбой с прокладкой из резиностойкой резины. Уровень масла замеряют маслоуказателем 14. Корпус обдувается вентилятором 6, закрытым кожухом 7.
1.4. Конструкции червяков и червячных колес
1.4.1. Червяки
Червяки обычно выполняют заодно целое с валом, но при большой разнице в диаметрах валов и червяков последние выполняют насадными.
По форме внешней поверхности червяки бывают цилиндрическими (рис. 3а), которые чаще используются, и глобоидными (рис. 3б).
Рис. 3. Типы червячных передач:
а – передача с цилиндрическим червяком;
б – передача с глобоидным червяком
Глобоидная передача имеет более высокий КПД, более надежна и долговечна, но из-за сложности изготовления имеет пока ограниченное применение.
Примером ее применения может служить рулевая колонка в автомобиле.
По числу заходов червяки бывают однозаходными и многозаходными ( - число заходов).
По направлению линии витка – с правым и левым направлением линии витка.
По форме винтовой поверхности резьбы цилиндрического червяка различают – архимедовы, конволютные и эвольвентные червяки.
Архимедов червяк в осевом сечении имеет прямолинейный профиль равнобедренной трапеции (рис. 4, а), аналогичный профилю инструментальной рейки. Угол между боковыми сторонами профиля витка у стандартных червяков . В торцовом сечении витки очерчены архимедовой спиралью.
Конволютные червяки имеют прямолинейный профиль в нормальном к витку сечении (рис. 4, б).
Эвольвентные червяки имеют эвольвентный профиль в торцовом сечении и, следовательно, подобны косозубым эвольвентным колесам, у которых число зубьев равно числу зубьев (заходов) червяка.
Наиболее распространены архимедовы червяки.
Рис. 4. Типы червяков: а - архимедов червяк;
б - конволютный червяк; в - эвольвентный червяк
1.4.2. Червячные колеса
Червячные колеса от цилиндрических косозубых зубчатых колес отличаются вогнутым профилем зубьев в осевом сечении. С целью экономии дорогостоящих сплавов цветных металлов колеса выполняют составными: центр из серого чугуна, иногда из стали, а зубчатый венец из бронзы или латуни. Для тихоходных малонагруженных передач при скорости скольжения используют относительно мягкие серые чугуны.
Зубчатые венцы с центрами соединяют посадкой с натягом и винтом (рис. 5, а); большие колеса (диаметр более 400 мм) без натяга только винтовым креплением. В крупносерийном и массовом производстве часто применяют заливку бронзового венца на чугунный или стальной центр (рис. 5, б), что позволяет снизить расход бронзы и латуни.
Рис. 5. Конструкции червячных колес.
1.4.3. Материалы червяков и червячных колес
В связи с большими скоростями скольжения и неблагоприятными условиями смазывания червячным передачам свойственно механическое изнашивание, заедание и задиры, поэтому материалы червяка и колеса должны составлять износостойкую антифрикционную пару с пониженной склонностью к заеданию и задирам.
Червяки изготавливают из углеродистых и легированных сталей. Архимедовы и конволютные червяки, шлифование витков которых вызывает затруднение, изготавливают из нормализованных или улучшенных сталей 40, 45Х, 40ХН и других с твердостью .
Нелинейчатые и эвольвентные червяки изготавливают из цементуемых сталей 20Х, 18ХГТ с твердостью , либо из среднеуглеродистых сталей 45, 40ХН, с поверхностной закалкой до твердости
.
Материалы, применяемые для изготовления зубчатых венцов червячных колес, в зависимости от антифрикционных свойств в паре со стальным червяком условно делят на три группы.
I группа – оловянные бронзы типа Бр010Ф1, Бр010Н1Ф1 и другие используют при больших скоростях скольжения (). Они дороги и дефицитны.
II группа – безоловянные бронзы, например, алюминиево-железистые типа БрА9Ж4, БрА9Ж3Л, а также латуни, например, ЛЦ23А6Ж3Мц2 и другие обладают повышенными механическими характеристиками, но имеют пониженные противозадирные свойства. Их применяют в паре с твердыми (Н>45HRС э) шлифованными и полированными червяками для передач, у которых .
III группа – чугун серый (СЧ15, СЧ20) применяют при и в ручных приводах.
1.5. Основные геометрические параметры червяка, колеса и червячной передачи
Основным параметром передачи является осевой модуль червяка, который для колеса является торцовым:
где р – шаг резьбы (зацепления).
Делительный диаметр червяка – диаметр цилиндра, на котором толщина витка и ширина впадины равны по величине,
,
где - коэффициент диаметра червяка, величина стандартная (ГОСТ 2144-76). Чем меньше модуль , тем больший коэффициент диаметра червяка следует назначать, чтобы обеспечить жесткость червяка (табл. 2).
Для червячных цилиндрических передач ГОСТом 2144-76 регламентированы:
– длина нарезанной части червяка, ;
– делительные углы подъема винтовой линии червяка и наклона зубьев колеса (табл. 3);
– межосевые расстояния,
Таблица 1
Стандартные ряды межосевых расстояний , мм
Для нестандартных передач не обязательно придерживаться ГОСТа. Межосевые расстояния можно округлять и за счет некоторого отклонения передаточного отношения от стандартного (табл. 4), за счет изменения числа зубьев колеса .
Для нарезания червячных колес и со смещением и без смещения используют один и тот же инструмент. Червячная фреза и червяк должны иметь одинаковые размеры, поэтому он не имеет смещения (у червяка изменяется диаметр начальной окружности, она не совпадает с делительной), а со смещением нарезают только колеса. При заданном межосевом расстоянии коэффициент смещения инструмента.
Швейцарская производственно-инжиниринговая компания ENCE GmbH (ЭНЦЕ ГмбХ) образовалась в 1999 году, имеет 16 представительств и офисов в странах СНГ, предлагает оборудование и комплектующие с производственных площадок в США, Южной Кореи, Канаде и Японии, готова разработать и поставить по Вашему индивидуальному техническому заданию червячные редукторы.
Описание и принцип работы
Другим представителем типов редукторов являются червячные редукторы, получившие свое название от применяемой в них червячной передачи. Червяком называют винт, являющийся составной частью передачи. Данный тип редукторов получил широкое распространение. Сфера его применения охватывает такие области как насосное оборудование, различное транспортировочное оборудование (конвейеры, подъемники и т.д.), приводы, а также станки для обработки металла, дерева и других материалов.
Червячные редукторы построены на базе червячной передачи, состоящей в свою очередь из зубчатого колеса, входящего в зацепления червяком - винтом со специальной резьбой.
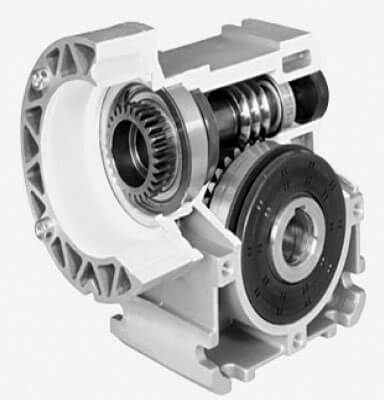
Червячные редукторы всегда понижающие и имеют разброс и высокую точность передаточных отношений. Передаточное отношение червячной пары может достигать 1-100 (иногда и выше). Подобное передаточное отношение может быть получено с помощью трехступенчатого цилиндрического редуктора, однако при этом червячное зацепление позволяет получить большую плавность хода и снизить уровень шума. Еще одно преимущество - простота и низкая стоимость червячных редукторов
Кроме того в червячных редукторах имеется уникальная функция самоторможение, то есть отсутствие обратимости - при полной остановке ведущего вала невозможно провернуть ведомый вал. Эта особенности проявляется при передаточных числах от 35, а точнее при угле винтовой линии червяка более 3,5 градусов.
Следует иметь в виду, что увеличение передаточного отношения сопровождается снижением КПД, по причине большего трения червяка об зубчатое колесо.
Привод имеет компактные размеры (в сравнении с цилиндрическими агрегатами).
Ресурс червячных приводов составляет, в среднем, 10 тысяч часов.
Червячная передача
Червячная передача состоит из винта с выточенной на нем резьбой и косозубого зубчатого колеса. Винт именуется червяком, что дало название передаче, а далее и типу редуктора. Вращательное движение червяка обеспечивает поступательное (вдоль оси винта) движение витков резьбы, находящейся в зацеплении с зубьями колеса. Зацепление между зубьями колеса и витками винта происходит по линии. Таким образом, передается усилие между элементами передачи. Оси червяка и колеса располагаются под прямым углом друг к другу.
Редуктором (червячным) называют механизм, который преобразует высокую угловую скорость вращения входного вала в низкую на выходном валу. При этом крутящий момент на выходном валу возрастает пропорционально уменьшению скорости вращения.
Редуктор (червячный) состоит из корпуса, в котором расположены зубчатые колеса, валы, подшипники валов, системы их смазки и др. Наличие корпуса обеспечивает безопасность, хорошую смазку и, следовательно, высокий КПД, в сравнении, например, с открытыми передачами.
Основные характеристики червячных редукторов
Основные характеристики редукторов: КДП, частота вращения входного и выходного валов, передаточное отношение, передаваемая мощность, количество ступеней и тип передач.
Передаточное отношение - это отношение скоростей вращений входного к скорости вращения выходного вала.
i = w вх /w вых
КПД редуктора определяется отношением мощности на входном валу к мощности на выходном валу
n = P вх /P вых
Редуктор
Червячный редуктор - универсальный корпус
Диаметр выходного вала D30
Различные устройства и механизмы для трансформации крутящего момента и изменения его направления используются с древних времён, но только современные редукторы способны справляться с теми нагрузками, которые необходимо преобразовывать человеку в 21 веке. Червячный редуктор является одним из таких «приспособлений» используемых для изменения передаточного числа вращения вала.
Данное устройство имеет достоинства и недостатки, но по сравнению с деревянными шестернями используемыми в Древнем Египте для орошения полей, червячный редуктор является совершенным устройством, во всех отношениях.
Преимущества червячных редукторов
Среди преимуществ этого механизма по трансформации крутящего момента можно выделить следующие достоинства:
Высокое передаточное число
Червячный редуктор позволяет передавать крутящий момент с соотношением до 1000/1, что практически невозможно реализовать при других технических решениях.
Компактность
Червячный одноступенчатый редуктор имеет небольшие габариты, поэтому данный механизм и двигатель могут быть объединены в одном корпусе.
Бесшумность
В сравнении с другими редукторами, червячный механизм производит меньший уровень шума во время работы.
Плавность хода
Передача крутящего момента посредством червячного редуктора, позволяет добиться идеальной плавности хода подключённых к данному устройству механизмов.
Отсутствие обратного хода
Если передаточное число червячного редуктора превышает значение 35/1, полностью отсутствует эффект «обратного хода». Ведущее колесо в этом случае невозможно провернуть и при небольшом угле подъёма червяка. Если данный показатель будет слишком мал, то блокировка обратного хода произойдёт и при меньшем передаточном соотношении.
Недостатки червячных редукторов
Данный механизм имеет и недостатки, которые накладывают значительные ограничения на использование червячной передачи, если мощность агрегата превышает 60 кВт. К недостаткам редуктора этого типа относятся:
Низкий КПД
В сравнении с другими устройствами по трансформации крутящего момента, КПД червячного редуктора значительно ниже, поэтому там, где не требуется высокая плавность хода и низкий уровень шума, данные механизмы не применяются по экономическим соображением.
Нагрев
Несмотря на то, что червячная передача находится в рабочей смазке в течение всего срока эксплуатации, все равно происходит значительный нагрев в результате трения металлического червяка и ведомой шестерни.
Особенно сильно этот нежелательный эффект проявляется, если мощность агрегата превышает 16 кВт.
Невозможно применить данную конструкцию, если мощность передаваемого крутящего момента слишком велика
Особенности конструкции, а также низкий КПД не позволяют использовать данное устройства для мощных установок. Наиболее распространённые механизмы, в которых реализованный способ червячной передачи крутящего момента не превышает значения 15 кВт.
Большой люфт между валами
Данная проблема проявляется при значительном износе червячного привода и имеет большее значение, чем в других видах передаточных механизмов.
Виды червячных редукторов
Червячные редукторы могут существенно отличаться в зависимости от области применения механизма.
Основные отличия, которые могут использоваться в конструкции:
- Разное число заходов;
- Материал детали;
- Направление резьбы;
- Профиль резьбы;
- Типами применяемого винта.
Данные отличия могут присутствовать в различных сочетаниях. Какие виды червячных редукторов использовать решает инженер на стадии проектирования и разработки устройств и механизмов, использующих такие типы передачи крутящего момента.
Проектирование червячного редуктора
Смастерить червячный редуктор своими руками практически невозможно. Расчёт червячного механизма должен осуществляться квалифицированным специалистом. Когда чертёж будет сделан, все детали по нему изготавливаются только из материалов надлежащего качества, иначе зубчатый механизм может выйти из строя после непродолжительной работы. Сборка червячного редуктора, также должна осуществляться опытным мастером. Несоблюдение этого правила может значительно снизить эксплуатационный ресурс детали, ведь кроме правильной установки валов, понадобится тщательная регулировка червячного механизма.
Если необходимо применение червячного редуктора для того чтобы установить самодельный механизм по передаче крутящего момента, то в это случае лучше использовать уже готовые б/у изделия от техники, в которой используется подобный вид передачи крутящего момента. В том случае, когда осуществляется самостоятельная разработка новых устройств, которые будут запатентованы, проектирование червячного редуктора следует заказать в конструкторском бюро, занимающемся подобными разработками.
Принцип работы
Основой всего передаточного механизма является червеобразный ведущий винт, в «честь» которого данные типы редукторов и получили своё название. Червячный винт взаимодействует с шестерней, осевой вал которой расположен под прямым углом. В результате такой сцепки происходит трансформация высокой скорости вращения входного вала с низким крутящим моментом, на вращение выходного вала с небольшой частотой, но значительно большим усилием. Компоновка червячного редуктора может быть различной. Если вал червячного редуктора вращается со скоростью ниже 5 м/с, то червяк располагается снизу, если скорость выше — то устанавливается редуктор с верхним червяком.
Большинство механизмов этого типа используются с одной передаточной ступенью, но иногда для регулирования соотношения может применяться двухступенчатый червячный редуктор.
Если скорость вращения вала более 10 м/с подшипники и гипоидные передачи должны смазываться под давлением. Если мотор тихоходный, то достаточно естественной циркуляции масла при вращении передачи.
Масло для червячных редукторов должно быть высокой вязкости, иначе процесс износа наиболее нагруженных частей редуктора значительно ускорится.
Ремонт редуктора
Несложный ремонт червячного редуктора можно осуществить собственными силами. Если мотор и привод объединены в одном корпусе, то следует аккуратно разобрать механизм.
Часть общего картера, в которой находится привод, также подлежит разбору. Если конструкция червячного привода изготовлена под высокоскоростной мотор, то, прежде чем приступать к разбору редуктора, необходимо слить трансмиссионное масло из корпуса.
В редукторе этого типа применяются высококачественные подшипники, поэтому наиболее часто необходимость ремонте возникает если шестерня и червяк изношены свыше предельных значений. Рабочая пара всегда подлежит одновременной замене на полный ремкомплект, который прежде чем поступить в торговую сеть, должен быть правильно подобран и испытан на специальном стенде.
Если износ червячной пары незначительный, то зазор можно ликвидировать, используя специальные шайбы-прокладки на ведомом валу.
Конструкция червячного редуктора также позволяет осуществить регулировку зацепления шестерни с червяком без разбора корпуса. Для этой цели используется болт, который встроен в корпус. Если имеется чертёж устройства, то можно без труда определить, где шестерня регулируется. Если чертёж отсутствует, то косвенным признаком регулировочного болта, будет наличие на нём контргайки, которая используется для фиксации отрегулированного зазора между червяком и зубчатым колесом. Крайне редко подшипники редуктора требуют замены. Обычно привод оснащается качественными шарикоподшипниками, которые не требуют замены или ремонта в течение всего эксплуатационного срока детали. Подшипники могут быть испорчены только в том случае, когда привод долгое время использовался без смазки или с применением некачественных смазочных материалов.
Профессиональные механики, а также инженеры занимающимися проектированием такого вида редукторов, не рекомендуют использовать червячный привод, если передаваемая мощность превышает 200 кВт. Конструкция червячного редуктора не позволяет справляться с таким нагрузками, по причине чрезмерного нагрева во время работы. Если мощность устройства находится в диапазоне от 60 до 200 кВт, то в этом случае также необходимо разработать чертёж, на котором будут обозначены принудительное охлаждение масла, и правильный подбор материалов, из которых будет изготовлены червяк и шестерня передаточного механизма.
Кинематическая система устройства должна быть изображена таким образом, чтобы вращение ведомого зубчатого колеса было расположено под прямым углом к вращению входного вала червяка. Также необходимо сделать точное описание каждой детали, которая используется в передаточном механизме. Подшипники следует также указать на схеме, а чертёж должен отображать диаметр посадочного места для них.
Работа червячного редуктора возможна в любых погодно-климатических условиях, но при эксплуатации устройства в северных районах страны, необходимо использовать специальные масла и смазочные материалы, которые не застывают при низких температурах.
Червячный редуктор — малогабаритный тихоходный механизм, поэтому если необходимо сэкономить рабочее пространство при значительном показателе передаточного соотношения, то данный агрегат будет вне всякой конкуренции среди других моделей редукторов.
Продолжительность работы - 4 часа
Цель работы: Ознакомиться с конструкцией червячных редукторов, червячных колес и червяков.
Принадлежности:
1 Модель червячного редуктора
2 Линейка измерительная
3 Рулетка измерительная
4 Ключи гаечные
5 Штангенциркуль
Правила техники безопасности:
1 Нельзя работать неисправным ключом или ключом несоответствующего размера
2 Снятые детали редуктора надо класть на стол так, чтобы они не могли упасть от случайного толчка
3 Нельзя подкладывать пальцы под вал колеса и крышку редуктора при их установке
Червячный редуктор - это механизм, служащий для понижения угловой скорости и увеличения вращающего момента и состоящий из одной или нескольких червячных передач, смонтированных в закрытом корпусе.
Рисунок 1 – Одноступенчатый червячный редуктор
Червячная передача состоит из червяка (1)(рис.1), короткого винта с трапецеидальной или близкой к ней резьбой и червячного колеса (2) с косыми зубьями дугообразной формы. Она применяется для передачи вращательного движения между валами с перекрещивающимися осями.
Корпус редуктора с целью облегчения сборки изготовлен в виде разъемной коробки. Он состоит из нижней части (3), называемой собственно корпусом (основанием) и верхней (4) крышки. Разъем выполнен горизонтальным. Корпус и крышка соединяются болтами (5). В верхней части корпуса имеется окно (люк) (6), через которое заливается масло и производится наблюдение за состоянием колеса и червяка. Оно закрывается крышкой (7), имеющей отдушину (8), предназначенную для исключения избыточного давления внутри корпуса по отношению к корпусному, возможного вследствие нагрева редуктора. При отсутствии отдушины, нагретый воздух при эксплуатации редуктора выдавливался бы вместе с маслом через уплотнения, и на корпусе образовались бы масляные подтеки.
Опорами валов (9) и (10) редуктора являются подшипники качения (11). Назначения опор - удерживать вращающиеся детали в нужном для правильной работы взаимном положении.
В зависимости от того, как расположен червяк по отношению к колесу различают редукторы:
– с нижним - при окружной скорости червяка V 1 до 4..5м/с (рис.2а);
– с верхним - при V 1 = 5м/с (рис.2б);
– с боковым расположением червяка (рис.2в, г).
Рисунок 2 – Схемы одноступенчатых червячных редукторов
Одноступенчатые редукторы находят применение в диапазоне передаточных чисел ί =8…6З.
В зависимости от формы внешней поверхности червяка передачи бывают с цилиндрическими (рис. З а, 6, в) глобоидными (рис. З г) типами червяков.
а - архимедов; б - конволютный; в - эвольвентный;
Рисунок 3 – Основные типы червяков
Червяки в большинстве случаев выполняют как одно целое с валом из сталей: среднеуглеродистой марок 40, 46, 50, легированных 40Х, 40ХН с поверхностной или объемной закалкой до твердости 45…50НРСа. Наилучшую стойкость передачи обеспечивают червяки из цементированных сталей (20х, 18ХГТ), имеющих твердость после закалки 58...53НРСа. Зубчатые колеса изготавливают как цельные (из чугуна) так и составные (центр стальной или чугунный, венец - бронзовый).
Выбор марки материала венца зависит ох скорости скольжения витков червяка по зубьям колеса и длительности работы. При V = 6...25м/с и длительной работе рекомендуются оловянные бронзы БрОДОЫ. При V =З...6м/с – алюминиево-железистые бронзы БрА10)К4Н411. При V = 2м/с червячные колеса можно изготавливать из серых чугунов марок С4 15, СЧ 18-36. 5.
Последовательность выполнения работы:
1) Ознакомиться с техникой безопасности и теоретическими сведениями, изложенными в методических указаниях.
2) Сделать эскиз предложенного редуктора, проставить обозначения: расстояние от основания редуктора до верхней точки вала колеса (В) и червяка (Б), диаметр вала колеса d в2 и червяка d в1
3) Разобрать редуктор:
а) отвернуть винт, снять крышку
б) вынуть червячное колесо с валом и подшипниками
в) вынуть червяк с подшипниками
4) Ознакомиться с конструкцией червяка и червячного колеса
5) Сделать их эскизы и снять следующие параметры:
–число заходов червяка Z 1
–число зубьев колеса Z 2
–шаг червячного зацепления Рх(Рt), мм; (рис.3)
–диаметр вершины червяка d a 1 ; (рис.З)
– диаметр вершины колеса в среднем сечения d a 2
–ширина колеса в 2
–длина нарезной части червяка в 1 (рис.З)
–наибольший диаметр колеса d am 2 (рис.1)
(1)
Полученное значение сравнить с табличным (табл.1).
7) Определить осевой модуль m x и коэффициент диаметра червяка q, и округлить до ближайших стандартных значений:
(2)
(3)
d 1 –делительный диаметр червяка
d 1 = d a 1 –2· h a ·m, мм (4)
h a – коэффициент высоты головки (h a =1, реже 0,8)
Таблица 1 – Стандартные значения m x , q, d w
m x | 2,5 | 3,25 | (3) | 6,3 | (6) | 12,5 | ||||||||
q | 12,5 | 1 ряд | ||||||||||||
7,1 | 11,2 | 2 ряд | ||||||||||||
3 ряд | ||||||||||||||
d w |
8) Определить передаточное число:
9) Результаты измерений и вычислений свести в таблицу 2
10) Собрать редуктор
11) Убрать рабочее место
12) Сдать отчёт
Таблица 2 – Характеристика зацепления
Параметры зацепления | Обозначение, размерность | Формула | Значение параметров | Примечания |
Расстояние от основания редуктора до верхней точки вала колеса | В, мм. | |||
Расстояние от основания редуктора до верхней точки вала червяка | Б, мм | |||
Межосевое расстояние | d W , мм | |||
Число заходов червяка | Z 1 | |||
Число зубьев колеса | Z 2 | |||
Шаг червячного зацепления | P x , мм | |||
Диаметр вала колеса | d в 1 , мм | |||
Диаметр вала червяка | d в 2 , мм | |||
Диаметр вершин червяка | d a 1 , мм | |||
Диаметр вершин в среднем сечении | d a2 , мм | |||
Наибольший диаметр колеса | d am 2 , мм | |||
Ширина колеса | в 2 , мм | |||
Длина нарезной части червяка | в 1 , мм | |||
Осевой модуль зацепления | m, мм | |||
Делительный диаметр червяка | d 1 , мм | |||
Коэффициент диаметра червяка | q | |||
Передаточное число | ί |
Контрольные вопросы:
1 Что такое редуктор? Каково его назначение?
1. Область применения червячных передач.
2. Из чего состоят червячные передачи?
3. Классификация червячных передач.
4. Классификация червяков.
5. Из какого материала изготовлен червяк?
6. Достоинства червяков.
7. Недостатки червяков.
8. Конструкции червячного колеса.
10. Из какого материала делают червячное колесо?
11. Отличие червячных колес.
12. Почему из мягких материалов изготавливают венец червячного колеса?
13. Какое передаточное число у червячной передачи?
14. Что такое «заходы» червяка?
Сколько заходов бывает у червяка?
16. На каких поверхностях нарезают червяки?